Understanding the productivity differences between drum type and batch mix asphalt plants is essential for contractors and project managers aiming to optimize their operations. Each type of plant offers distinct advantages and disadvantages that can significantly impact overall efficiency and output. This article explores the key differences in productivity between these two asphalt production methods, helping stakeholders make informed decisions based on their project needs.
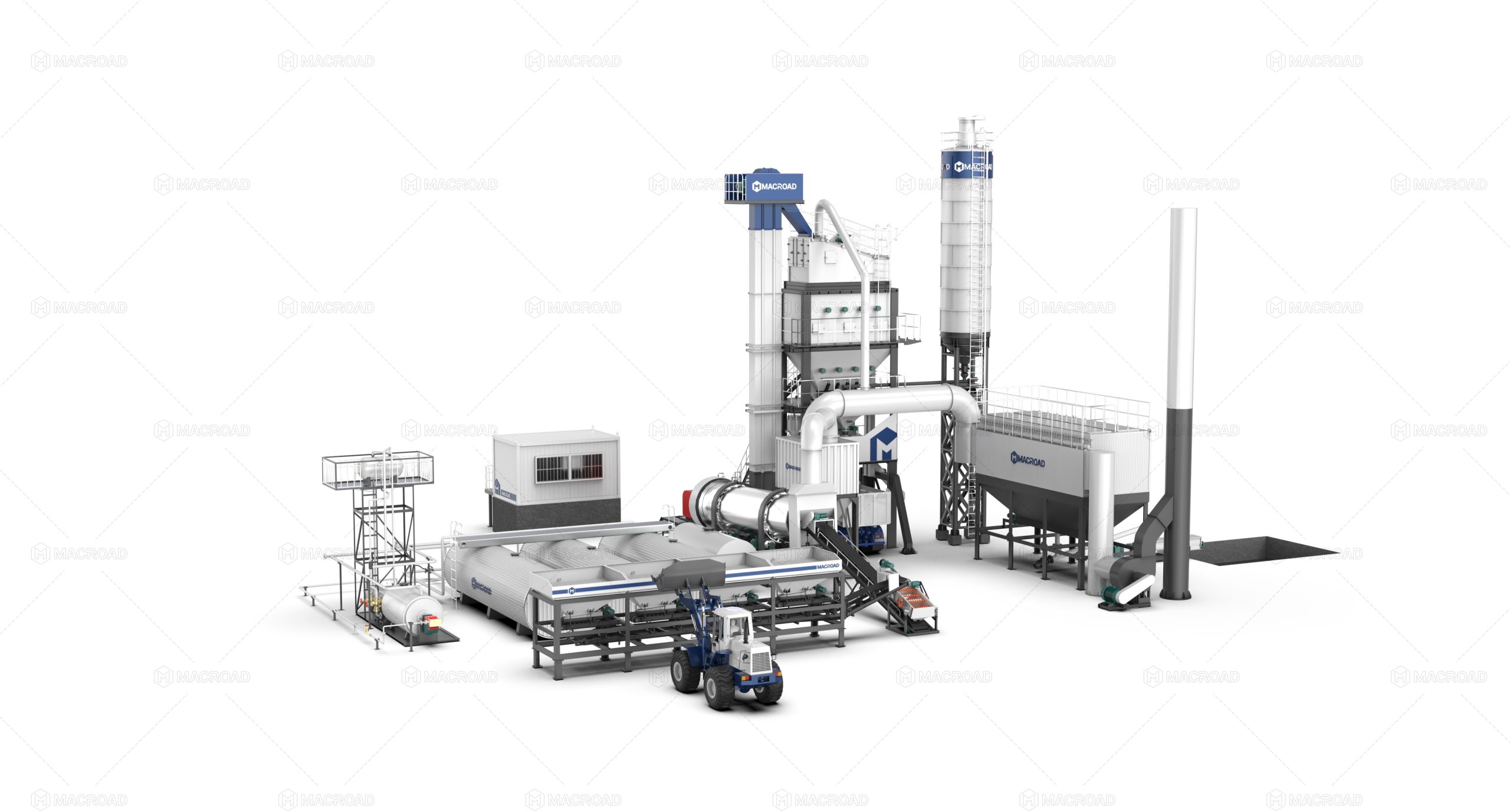
Drum Type Asphalt Plants: Continuous Efficiency
Drum type asphalt plants are designed for continuous production, which makes them particularly efficient for large-scale projects requiring high volumes of asphalt. These plants operate on a streamlined process where aggregates and asphalt binder are mixed continuously as they move through the drum. This design allows for a rapid production cycle, often yielding a consistent output of asphalt every few minutes.
The inherent efficiency of drum plants stems from their ability to produce asphalt without the interruptions typical of batch processes. Once the plant is set up and calibrated, it can maintain a steady flow of material, reducing downtime associated with loading and unloading. As a result, drum type plants can achieve production rates significantly higher than batch mix plants, making them ideal for large infrastructure projects, such as highway construction or major road repairs.
Moreover, the continuous nature of drum plants allows for greater flexibility in material usage. Contractors can often switch between different asphalt mixtures with minimal disruption, which is beneficial for projects that require various asphalt types. This adaptability can enhance productivity by reducing the time spent on transitions between different mixes.
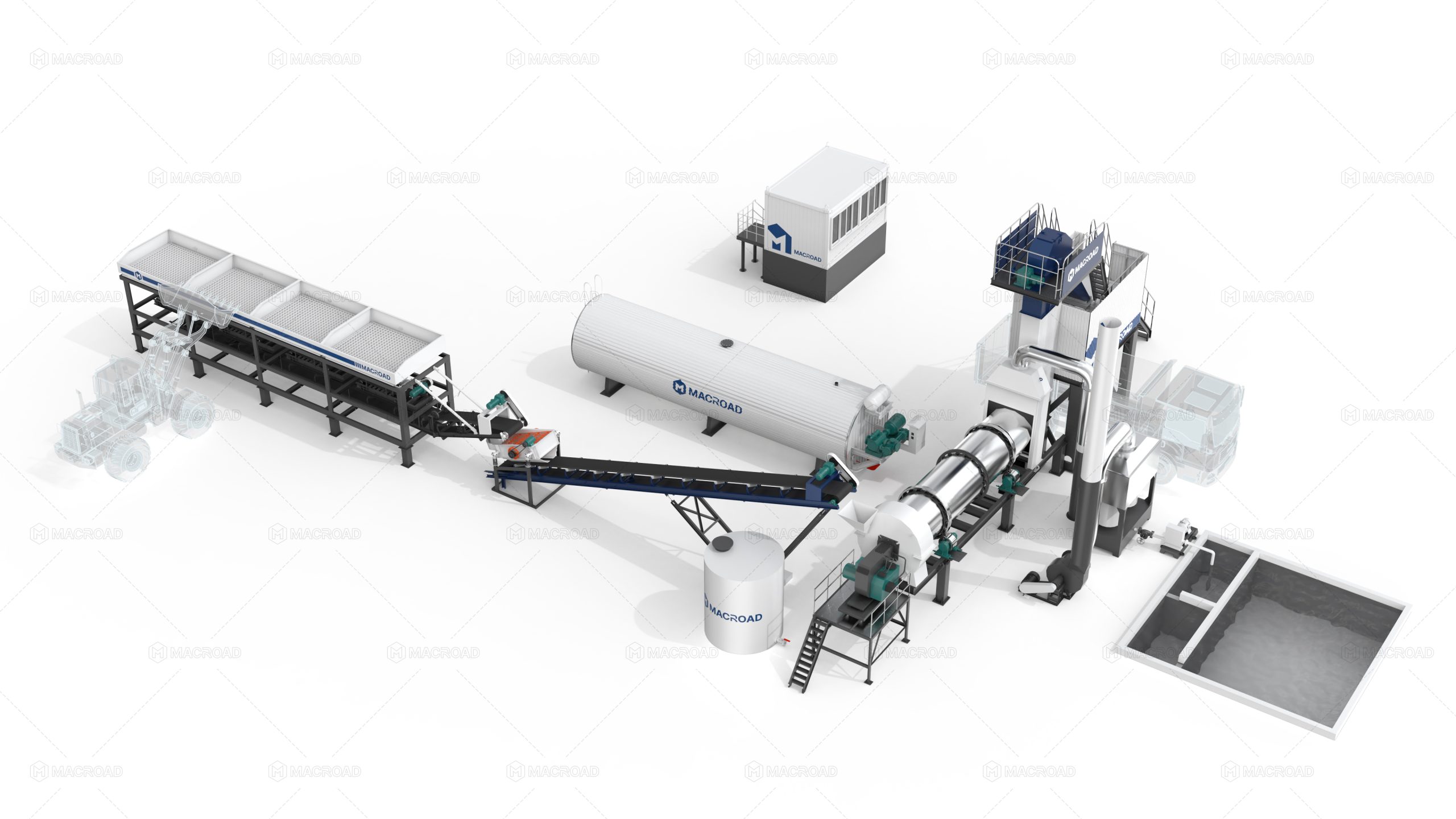
Batch Mix Asphalt Plants: Precision and Quality
In contrast, batch mix asphalt plants operate on a discrete cycle, producing asphalt in batches rather than continuously. Each batch requires a specific amount of time for weighing, mixing, and discharging, typically taking around 40 to 60 minutes to complete. While this process allows for precise control over the asphalt mix and ensures high-quality output, it also introduces potential inefficiencies.
The productivity of batch mix plants can be affected by several factors, including the complexity of the asphalt mix and the need for meticulous quality control. Complex mixes that incorporate additives or specialty materials may require longer mixing times, further extending the batch cycle. Additionally, the need to clean the mixing equipment between batches can also contribute to downtime, impacting overall output.
Despite these challenges, batch mix asphalt plant is often favored for projects where quality and mix customization are paramount. The ability to control the exact proportions of materials allows contractors to produce specialized asphalt formulations that meet specific engineering requirements. For projects prioritizing quality over quantity, batch mix plants can provide the necessary precision, albeit at a lower production rate compared to drum type plants.
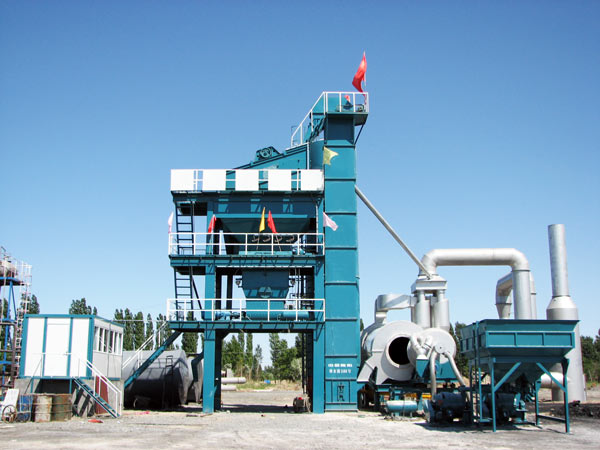
Selecting the Right Plant for Your Project
There are many types of asphalt plants, when choosing between drum type and batch mix asphalt plants, understanding the productivity implications is crucial. For large projects with high asphalt demands, drum type plants typically offer the best solution due to their continuous production capabilities and higher output rates. The efficiency of these plants can lead to significant time and cost savings, particularly for contractors working on tight schedules.
On the other hand, if the project requires specialized asphalt mixtures or a focus on quality, batch mix plants may be the better choice. While they may produce asphalt at a slower rate, the precision and control they offer can yield superior results, ensuring that the final product meets all necessary specifications.
Conclusion
Ultimately, the decision should be based on the specific needs of the project, including factors such as production volume, mix complexity, acceptability for asphalt mixing plant price and quality requirements. By carefully evaluating these aspects, contractors can select the most appropriate asphalt production method, optimizing both productivity and project success.
In summary, the productivity differences between drum type and batch mix asphalt plants are significant and depend on the nature of the project. Drum type plants excel in continuous production and higher output, making them ideal for large-scale projects. Conversely, batch mix plants provide precision and quality control, essential for specialized applications. By understanding these differences, contractors can make informed decisions that align with their project goals, ultimately leading to successful outcomes in asphalt production.